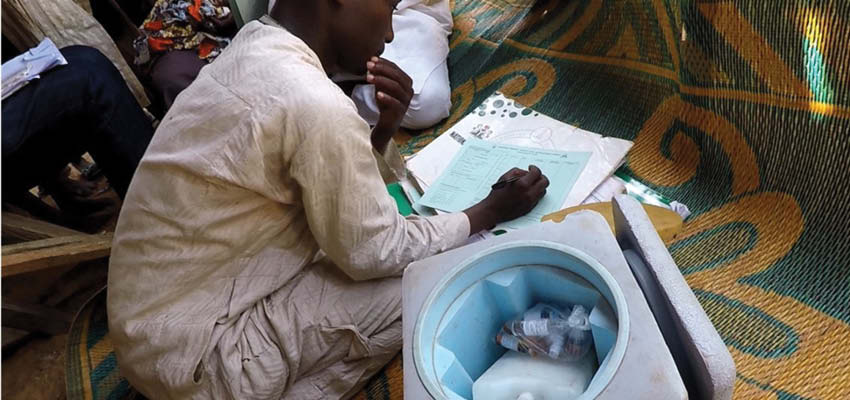
Redesigning the existing SMILE carousel to be injection moldable to reduce cost at volume.
MIT D-Lab class
Community partner
- Kitty C. Liao
Country
Cameroon
Student team
MIT students unless otherwise noted.
- Kevin Tang ’25, MDes, Harvard
- Shua Chu ‘25, Mechanical Engineering
- Kaili Glasser ‘24, AMDP MEng
- Yutong Zhang ‘24, AMDP MEng
Project description
In the realm of vaccine delivery, the "last mile" remains a critical challenge. Current cold-chain equipment struggles during this final leg, leading to freezing vaccines or failing to maintain the required temperature (2-8 degrees C, 35.6-46.4 degrees F). Notably, 76% of cold-chain equipment vaccine deliveries in Cameroon did not meet the WHO's temperature requirements. Human errors compound the issue, accelerating vaccine spoilage.
The current prototype of SMILE developed by Kitty C. Liao is a transportable insulated spinning carousel cold-box, offering enhanced functionalities by securing, isolating, and organizing vaccines during transportation. SMILE's single ice pack extended cooling times to 103-120 hours (4.2 days), whereas the WHO carrier managed only 4 hours. A significant 76% of health workers expressed a preference for SMILE over existing carriers/cold boxes.
Despite SMILE's success, the current carousel prototype faces manufacturing challenges. Costing $1,175 per unit with the CNC-manufactured carousel assembly in each SMILE contributing to $700 of the total cost per unit, it demands redesign for manufacturing and cost accessibility.
Solution including technical details
We’re able to decrease the manufacturing cost of the carousel in SMILE to $22.2 per unit by splitting the original design into symmetric, injection moldable pieces in order to minimize the number of unique molds required. We moved the grooves that hold the vaccine holders from the cylinder to the top/bottom and also removed the cylinder part in the center to minimize weight without sacrificing function. Besides, we separated the “butterfly” and comb parts to allow the butterfly parts to be manufactured through die cutting, which is a much cheaper process to implement. The thermal tests show similar thermal performance between our solution and the previous carousel design.
[Caption] Collection of SMILE Prototypes
[Caption] Setup for Thermal Test of New Carousel Design
[Caption] Final Prototype of New Carousel Design
Hand-off to partner, next steps
For next steps, we recommend further evaluating the tolerance for comb and carousel design for injection molding as all the prototyping are done by 3D printing. More tests should also be done, including drop tests and vibration tests to ensure the strength of the structure of ghost carousel design after the cylinder is removed. A usability test, with cyclic loading and unloading vaccines, should also be the next step to test the attachment between the comb and butterflies.
Contact
Macauley Kenney, D-Lab: Design for Scale Instructor
Yutong Zhang, MIT ‘24, z