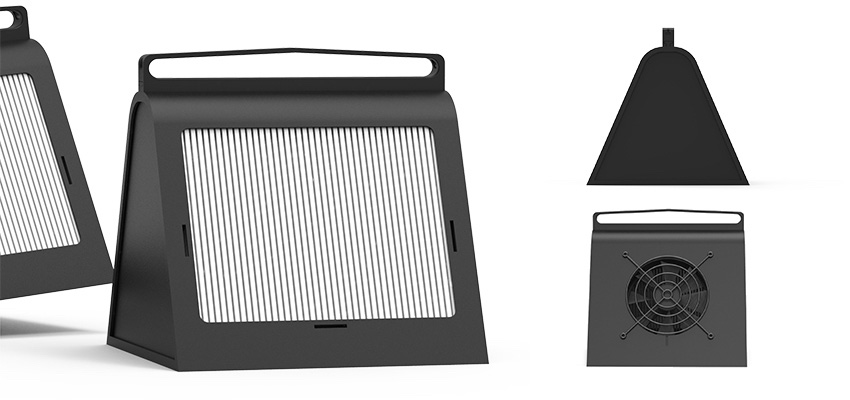
Advancing the design, manufacturability, and usability of a low-cost air purifier aimed at improving the air quality in Hong Kong’s subdivided flats.
Student team
- Saloni Bedi, MIT ‘23, M.S. Integrated Design and Management
- Connie Ly, MIT ‘24, B.S. Mechanical Engineering
- Zach Sternberg, MIT ‘23, M.S. Integrated Design and Management
- Brandon Worrell, MIT ‘24, B.S. Mechanical Engineering
Community partner
- NG Aik Min, Senior Project Officer at the Office of Service-Learning (OSL)
- Lingnan University, Tuen Mun, Hong Kong (aikminng@ln.edu.hk)
Location
Hong Kong
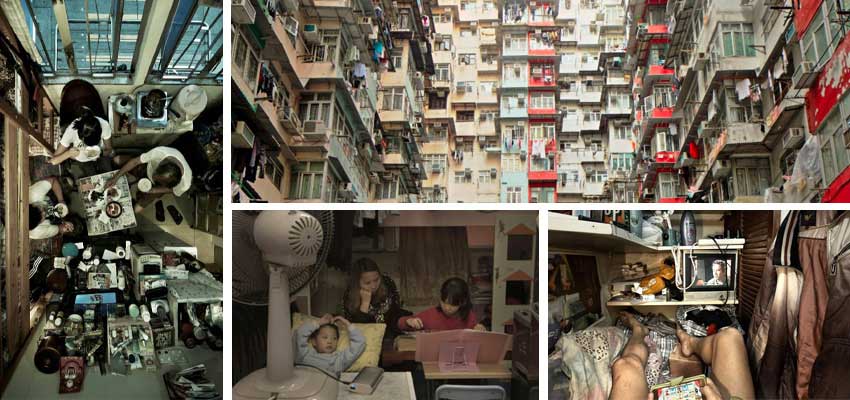
Project description
Over 220K people live in subdivided units (SDUs) in Hong Kong which are cramped with multiple constantly exposed to poor air quality, circulation, and odors. Our D-Lab team partnered with Lignan University to further develop their concept for a low-cost air purifier to be manufactured at scale and distributed to residents. While small fans exist at low price points and portable air purifiers for high-end clientele, there is a market gap that can be addressed by making a compact air purifier that can be effective in these small spaces, which are often under 120 square feet.
The initial Lignan prototype was made of laser-cut particle board, glued together into a box containing two high-efficiency particulate air (HEPA) filters and a computer fan powered by rechargeable USB battery pack. While this design can easily flat-pack, it would not be feasible for users to assemble and glue the puzzle-shaped pieces together.
In order to overcome these feasibility challenges, we took a step back and iterated on designs for the housing. We sought to improve the user-friendliness, compactness of the final product, compactness of the product during transportation, and durability. After in-depth brainstorming and assessment, we moved forward with a new triangular prism-shaped design.
Video: Animation showing the optimized assembly of the triangle prism-shaped design inclusive of factory assembly prior to distribution as well as user assembly.
The triangle prism-shaped design for the air purifier is made up of three main injection-molded plastic components: (1) the primary shell, (2) front and back triangular walls, and (3) the handle. The primary shell is a single component divided into three walls that fold into the triangle shape. Each of the three panels of the component held the fan, the battery, and the HEPA filter respectively. In our initial prototype, the shell was three separate pieces fastened together with metal rods to create a hinge before being upgraded to a single piece with a “living hinge.” Identical triangular walls are inserted into tracks and compressed into place when the shell is folded to fully enclose the unit; these side walls originally snapped into place from the exterior, and were improved to increase durability. To hold the unit together, a D-Lab Design for Scale, MIT EC.729 Fall 2022 handle slides into a top rail. The handle also allows for portability, like a lunch box, or for the unit to be hung from a hook.
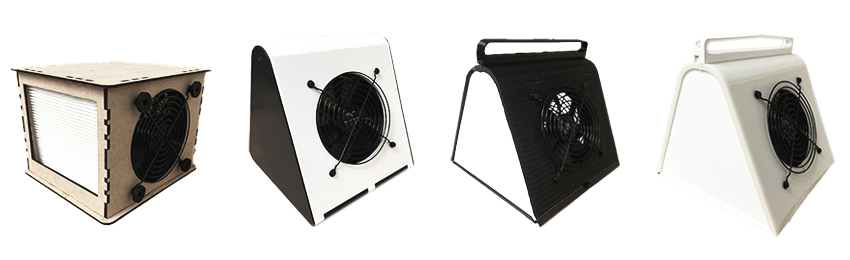
The prototypes were all 3D printed following DFM guidelines for injection-molding such as consistent wall thickness, no undercuts, and draft angle. However, large flat sheets might be more cost effective to thermoform at our targeted volume. Therefore, we also designed a negative for thermoforming and tested that manufacturing method as well. Further investigation into the cost is required due to the post-processing required in thermoforming, namely die cutting the holes and the addition heat application required to create the living hinges.
Next steps
Next steps for the design include further testing, cost analysis, and further refining DFM. Efficacy tests were performed at MIT to compare Lignan’s prototype to the triangle design. Our design removed PM2.5 and PM10 at comparable rates to the initial prototype and the battery did not overheat when run for extensive periods of time, however there is still room for more robust testing to confirm pressure drop and HEPA filter lifespan. Additionally, quotes have been pulled for local production here in the US, but further investigation is required for production in Shenzen, where our project sponsor has recommended manufacturing. Lastly, the thermoformed design would need to be further refined to ensure its feasibility and viability as the preferred manufacturing method.
MIT D-Lab Class
Contact
Emily Young, Co-Instructor Design for Scale
Macauley Kenney, Co-Instructor Design for Scale