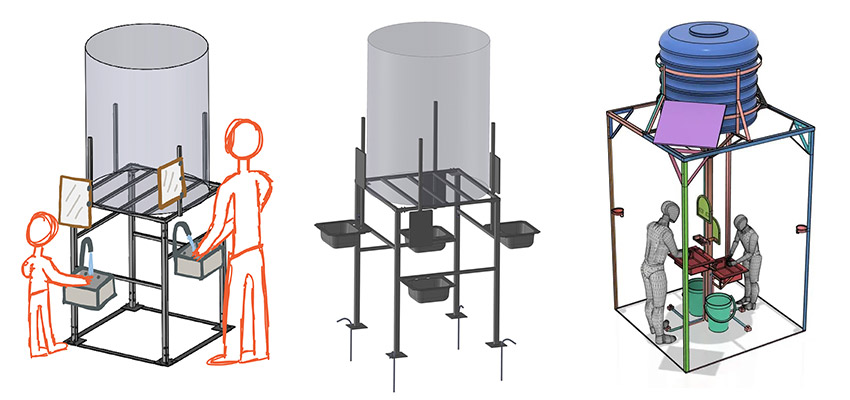
Redesigning the metal frame of Bioforge’s hand washing station to reduce the total cost of the product.
Student team
MIT students unless otherwise noted.
- Faith Bulan, '24
- Joushua Padilla, SM '23
- Christian Landis, M.S. EE, JHU, 2024
- Mohamed Othman, MEng 2023
- Edward Finman, SB 2024
Community partners
- Raphael Choudhury - Co-Founder
- Ju-un Choudhury - Co-Founder
- Kuldeep Aryal - Brac Partner
Location
Bangladesh (specifically Cox Bazaar, Bangladesh, where there is a refugee camp of almost 1 million people)
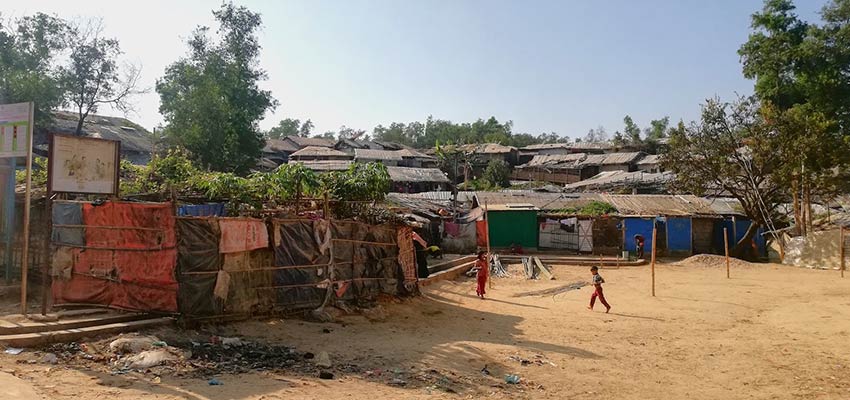
Context
Almost one million ethnic Rohingya refugees have arrived since 2017 in Cox Bazar, Bangladesh, seeking safety from targeted violence by the government of Myanmar. One of the main issues the refugees experience in the camp is water scarcity. Each tap in the camp is shared by over 150 families, consisting of four to five people each. Taps only dispense water for a few hours a day, and people rush or cut the line to ensure they get water. These actions lead to aggressive confrontation, and fights can happen over access to water.
The challenge
To combat water scarcity, Bioforge Health Systems, a company in Bangladesh that focuses on health technology, is developing a handwashing station with a 1000 L tank to provide water to refugees even when their tap is off. It also has human-centered design components like mirrors and sinks at multiple heights to encourage users to build the habit of washing their hands.
The main downside is that the system costs $1,200 USD, which is much more expensive than other hand washing stations on the market. The most expensive component is the steel frame that suspends the 1000 L tank 6 feet in the air, and it costs $500. The challenge for the students was to redesign the station’s frame to reduce its cost while maintaining safety and the product’s human-centered design components.
Brief note on competitors
Hand washing stations currently on the market cost anywhere from $50-$300, and they typically hold 40 - 50 L of water, with a maximum of 150 L. The main issue with these stations is that once the water runs out, it is never refilled. So, each station has a short life-span and cannot impact a community in the long term.
Technical solution
The students’ final solution is a metal structure that elevates the water tank four feet in the air. It consists of nine welded steel components: one platform for the tank, two H-shaped side walls, two horizontal bars to connect the side walls, and 4 posts to keep the tank on the platform. This design enables the frame to be flat packed and assembled on site. The design also keeps the 1000 L tank of the original design as well as the mirrors and multi-height sinks as human-centered design components.
The station has a safety factor of 3.0, which meets the standard set by the American Water Works Association for welded steel water storage structures. The structure will be staked to the ground through ground anchors (recommended), but long rebar stakes will work if needed.
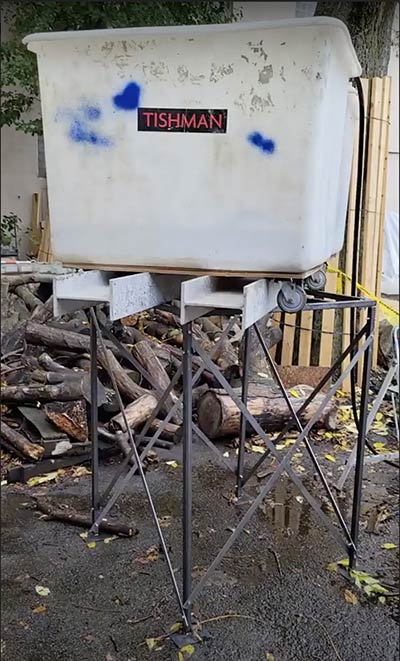
static load test of 850 kg, or 85% of the total expected load. Credits: MIT D-Lab Bioforge Team.
Final deliverable and next steps
The team recommends that Bioforge’s next steps are to conduct two tests: water flow testing through an open-source foot tap and user testing with the refugees.
The final deliverable, determined by the project sponsor, will be the CAD (computer aided design) files for the frame as well as a specifications document (bill of materials, engineering drawings, and critical dimensions), a manufacturing document, and an assembly guide.
MIT D-Lab Class
Contact
Emily Young, Co-Instructor Design for Scale
Macauley Kenney, Co-Instructor Design for Scale