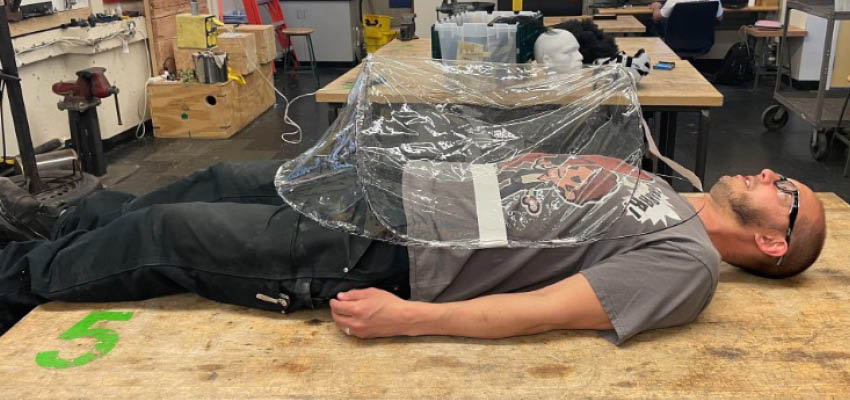
Developing a smaller SurgiBox design that optimizes its critical features for high-occuring minor surgical procedures.
MIT D-Lab class
Student team
MIT students unless otherwise noted.
- Alexandra Lee '25 - Alexandra is a Junior in Mechanical Engineering and is interested in Medical Technology and Innovation.
- Livia Zhang '24: Livia is a Senior in Mechanical Engineering specializing in product and game design.
- Samiksha Singh '27: Samiksha is a first-year at Wellesley College, interested in design and medical technology (undecided major).
- Brandon Worrell '24: Brandon is a Senior in Mechanical Engineering pursuing a career in the field of product design.
- Grace Hutter '25: Grace is a Junior studying Mechanical Engineering with a concentration in Biomechanics, while on a Pre-Medicine track.
Community partner
- Debbie L. Teodorescu, MD, SurgiBox Founder and Board Member
- Mike H. M. Teodorescu, PhD, SurgiBox CEO and Board President
- Atif Rakin, SurgiBox Chief Technology Officer, QM
Country
Global
Project overview
Surgibox, a portable sterile surgical system, provides a solution for conducting surgeries in remote or under-resourced settings. However, the current model of SurgiBox is not well-suited for minor procedures. Surgeons operating in the field often encounter challenges associated with transporting and setting up equipment themselves, and have highlighted the need for a smaller SurgiBox design, maintaining its critical features while addressing these challenges effectively.
Doctors in resource-constrained environments or during medical missions in remote areas need the ability to conduct surgeries with minimal equipment and infrastructure.
Our solution is the SurgiBox Mini, a compact and lightweight surgical enclosure that pops up and is designed to optimize critical dimensions while prioritizing visibility and comfort for surgeons. We started by brainstorming ideas that would help us preserve the functionality of the larger bubble while reducing the size. Based on our ideation sessions, we identified two design ideas to evaluate with our Pugh chart criteria.
The team divided into two and worked on creating rough prototypes based on both the design ideas. Based on partner feedback and testing, we decided to move forward with the popup design. Our next challenge was determining what material would be best for the frame, as we learnt from partner interviews that the model and popup functionality had to maintain a two-year shelf life.
Other important things that came up were the requirement of minimum four arm holes, high clarity and top visibility along with comfortable surgical spacing and structural stability. Additionally, we wanted to test out multiple pop-up designs to determine the best fit for our design requirements. Based on these criterias, we introduce our solution: the SurgiBox Mini. Constructed from spring steel and TPU plastic, it offers durability and flexibility, ensuring reliable popup performance in the variety of environments it will be deployed. Unlike the original SurgiBox, which requires a setup time of two minutes, the SurgiBox Mini significantly reduces setup time, offering a more streamlined solution for many procedures.
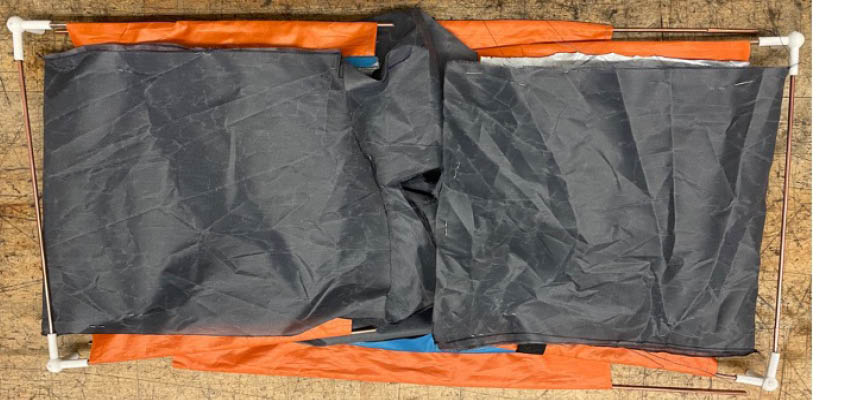
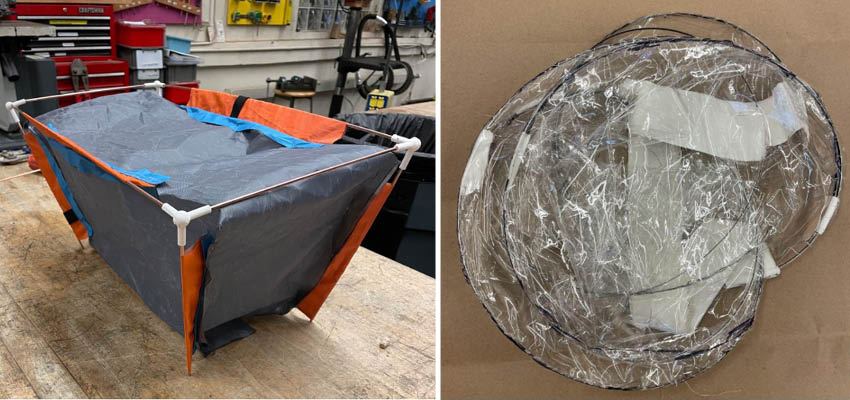
Next steps
The next steps for the SurgiBox Mini involve additional testing and refinement of the prototype. This includes the addition of lights and blood drip banks, features and feedback from the original SurgiBox design. Additionally, collaboration with manufacturers will be crucial to determine how to bring our prototype and design to market. The manufacturing is important to source materials and create manufacturing processes while ensuring that key design requirements are met. This process will involve rigorous testing and evaluation to ensure that the SurgiBox Mini meets the needs of surgeons in the field effectively.
Contact
Ankita Singh or Eliza Squibb, Co-Instructors D-Lab: Design