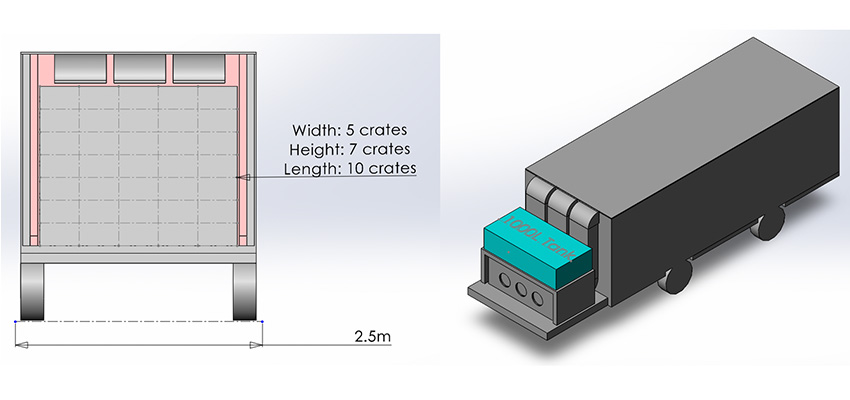
Problem framing
Currently, 40% of fruits and vegetables grown in Nigeria are lost between when they are harvested and when they arrive at the market (Nigeria: Food Smart Country Diagnostic, World Bank, 2020). One of the country’s most grown crops, tomatoes, suffers especially from post-harvest losses, with 76% of tomatoes being lost before reaching the market. Over half of this loss is attributed to poor transportation, handling, and storage practices (Nigeria: Food Smart Country Diagnostic), therefore we are focused on reducing post-harvest losses through the implementation of produce precooling technology.
Alyx Limited, a company which operates a cold chain logistic network for the Nigerian agricultural industry, offers farmers mobile refrigerated units that reduce post-harvest loss. These trailers precool the tomatoes by lowering their temperature from around 40℃ to around 15℃ within the span of one day. The company then moves the tomatoes to giant refrigerated trailers which transport them to the market. Unfortunately, few farmers are using Alyx Limited’s trailers because of the cost and power consumption. These trailers are expensive because they use generators and air conditioning units. Alyx Limited also asked us to minimize the trailer’s weight and increase its capacity so that it can traverse rough terrain easily and be more profitable.
Our focus
We are focused on designing a mobile storage unit which reduces field heat while satisfying Alyx Limited’s requests. More specifically, we are determining if it is feasible to use forced air evaporative cooling in a mobile application. This evaporative cooling system uses fans on the exterior to blow hot, dry air from outside through a wet evaporative cooling pad housed at the top of the chamber. The cool, humid outlet air is then pushed through crates of produce on either side of the chamber before exiting through exhaust channels located at the side walls of the container. A representation of this concept is shown below in figure 1.
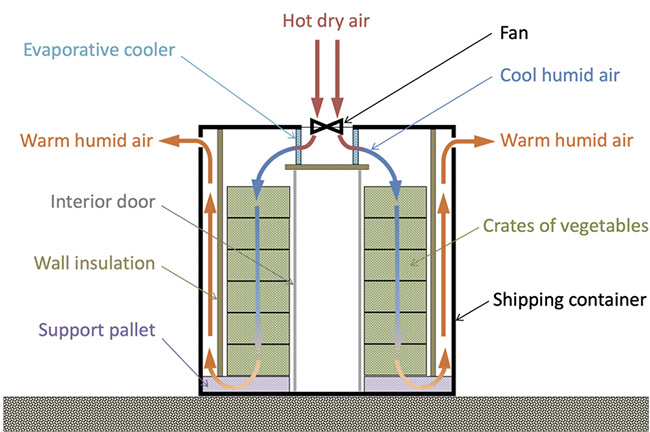
According to past research, forced air evaporative cooling is capable of quickly lowering tomato temperature and providing a humid environment to prevent tomato spoilage (Evaporative Cooling Technologies for Improved Vegetable Storage in Mali, MIT D-Lab 2021. We therefore focused on determining if the water requirements of the concept could be feasible for a mobile platform while ensuring the profitability of the unit.
Our evaluation
With the guidance of our community partner, we decided to implement a 5 x 10 x 7 crate configuration in order to contain a total of 350 crates of produce. This was determined to be a suitable carrying capacity for the economic feasibility of a mobile cooling unit. Physical obstacles, such as low hanging tree branches and the width of roads, were identified as limiting factors when determining the unit’s height and width. It was also decided to place the fans and cooling pads near the front of the trailer and use a ducting system to ensure ample airflow to all produce.The water tank was positioned above the cooling pads, with plans to utilize a solenoid valve to control the water flow to the cooling pads. Gravitational driving of the water was chosen over pump-driven flow following the experiments and recommendations of a prior team working on this concept (Wu, Isaacs, et al. (2021) “Evaporative Cooling Container for Fruits and Vegetables”. Massachusetts Institute of Technology).
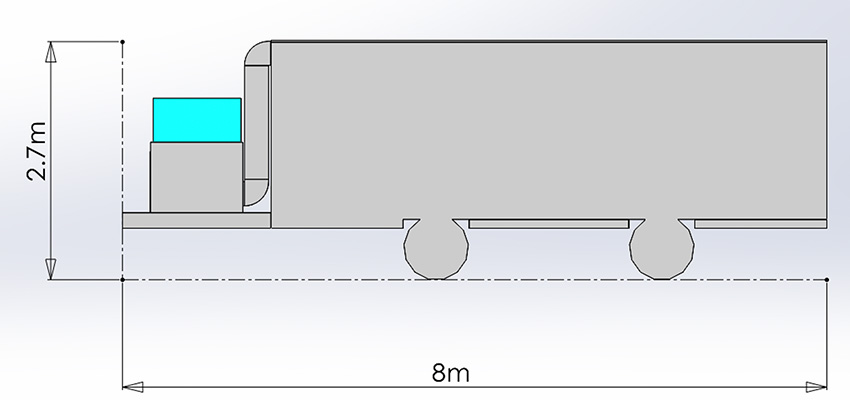
After determining the configuration, we then used simulation results from Frey to interpolate for the water requirements of a 350 crate configuration. The mobile system is designed to achieve a temperature drop from an ambient temperature of 33℃ to 25℃ within 8 hours of operation. For these system specs, it was found that 850L of water would be required to cool the tomatoes, which was then raised to 1000L when incorporating a safety factor. The total weight of the system is estimated to be similar to designs currently in use by our community partner.
MIT D-Lab class
Introduction to Energy in Global Development
Student team
MIT students unless otherwise noted.
- David Hernandez, ‘23, Mechanical Engineering
- Christine Padalino, ‘22, Chemical Engineering
- Maëlle Sardet, G, Mechanical Engineering, MEng
- Christine Tang, ‘25, Mechanical Engineering
Community partner
Alyx, Limited (Nigeria)
- Alexander Isong, CEO
Contact
Eric Verploegen, MIT D-Lab Research Engineer; Instructor, Introduction to Energy in Global Development
Christine Tang, Student Team member