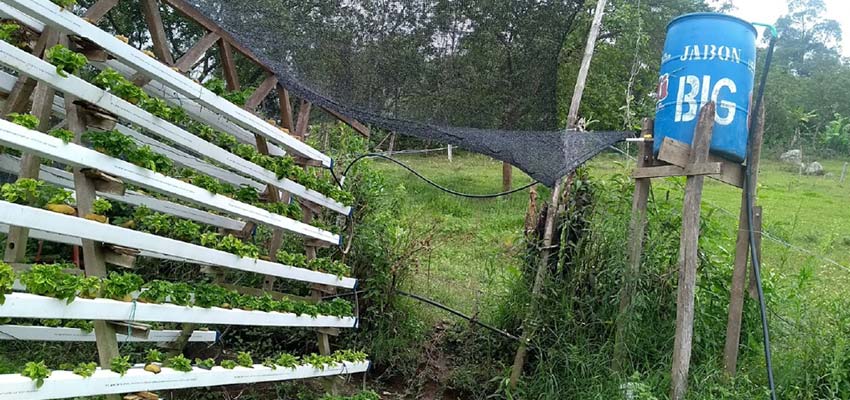
Sponics is a low-tech hydroponic system for coffee farmers in rural Colombia looking to improve their subsistence vegetable growing setup. It helps farmers save space, conserve water, maximize yields, preserve their farmland and ecosystem, and extricate them from the intensive labor of traditional farming.
Project Inception
In Colombia, 24% of the population is rural; 81% of this population are small farmers who have less than 2 hectares of land and are responsible for producing 83.5% of the food consumed by Colombians. Smallholders face a variety of challenges, including the need to optimize space, diversify and expand agricultural production, and adapt to increasingly variable climatic conditions.
Situated in the village of Guavio Alto, Colombia, Franklin Espitia is a coffee farmer of the De Finca association and a prolific inventor widely renowned in his community for building innovative farm machinery in resource-constrained settings. He has created several contraptions to diversify and enhance the productivity of his farm, one of which is a vertical hydroponic farm for spinach growing. Looking for technical solutions to troubleshoot the structure, fertilization, automation, and power source for his hydroponic setup, Franklin connects with D-Lab student researchers through Diversa for a co-creation project.
The current hydroponic setup. Photo: Kevin Fonseca.
Challenges and Solutions
During the stakeholder meetings, we defined four core challenges thwarting the functionality of Franklin’s hydroponic farm and planned research deliverables according to his available resources.
Schematic of fully automated hydroponic system, structures marked in black represent the current prototype, colored parts represent our additions. Credit: MIT D-Lab/student team.
-
Structural Optimization
Challenge: Increase the structural integrity and modularity of the hydroponic system.
After conducting an overview of 6 types of viable hydroponic structures, we identified the more ideal systems given the budget, technology, and environmental factors at De Finca that could be integrated with Franklin’s A-frame nutrient film technique (NFT) structure to utilize free space. We optimized the existing NFT setup by calculating the ideal flow rate and designing a malleable contraption to adjust the channel slope in response to the growing roots. We also introduced Franklin to hydroponic environment control mechanisms -- greenhouse and grow lights -- for regulating temperature, lighting, and pests.
-
Fertilization
Challenge: Identify the most ideal hydroponic feeding formulas that’s compatible with the plants’ needs. Effectively monitor the content and concentration of the nutrient solution throughout different stages of spinach growth.
We compiled a detailed hydroponic growing and maintenance toolkit for Franklin, who requested that we translate our research deliverables on fertilization into a procedural guide for him to study. He will have the formula of the primary nutrients needed for spinach growth, as well as tips on monitoring the nutrients with a digital pH/EC/ppm meter.
-
Pump Automation
Challenge: Automate the motor controls for the pump responsible for circulating nutrient solution across the hydroponic system. Protect the pump by monitoring water level and preventing circuit overflow.
We opted to use Arduino Nano to control a relay switch to turn the hydroponics pump on and off.We embedded a water sensor to detect water level in the collector tank so the Arduino knows when to pump water out of the collector tank into the feeder tank. We wrote software to automate this process and created an electronic wiring diagram for Franklin’s reference.
Left to right: Arduino wiring diagram; software testing setup; code samples for timing and sensor-based pumps. Photo: MIT D-Lab/student team.
-
Solar Power
Challenge: Implement an alternative energy system, preferably solar, to power the pump when the farm’s grid power supply experiences outages.
We resolved this issue by ideating a low-budget solar panel setup with a battery. The battery is also connected to the grid and charges when the grid power supply is functioning. In the future, if the solar panel generates any excess electricity, it could be directed to the industrial grow lights within the greenhouse to provide the seedlings with extra full-spectrum light exposure.
Future Direction
As some of our team members focus on solving immediate pain points with pump automation and fertilization, others go beyond Franklin’s baseline expectations to introduce structural optimization and alternative energy sources. Though Franklin doesn’t currently have the capacity to implement our long-term propositions due to busy farmwork, he has expressed tremendous interest in incorporating our suggestions into his next prototype. Some of our future visions include:
-
Increase the density of grow tubes to maximize yield, so that each family of De Finca can sustain themselves from less than 50 square meters of land with diverse hydroponic crops.
-
Improve the replicability of the hydroponic setup, modularize the design to promote it in the town of Fusagasuga and the nearby region of Sumapaz.
-
Identify business opportunities to establish contracts with organic stores and increase the farmers’ revenue. A case study is already being done with vertically grown baby spinach which is less complex to cultivate.
We are committed to being available to Franklin and his community through our Whatsapp group and responding to any questions they may have during future iterations of this project.
MIT D-Lab class
Student team
MIT students unless otherwise noted.
- Michael Lu '23, Electrical Engineering & Computer Science
- Nicole Jacobsen '23, Chemical Engineering
- Delight Nweneka '23, Biological Engineering
- Franny Xi Wu, '22, Wellesley College, Architecture, Urban & Development Studies
Community partners
- Natalia Barrera Gutierrez
- Kevin Fonseca
- Franklin Espita
Contact
Libby Hsu, MIT D-Lab Associate Director for Academics, Lecturer