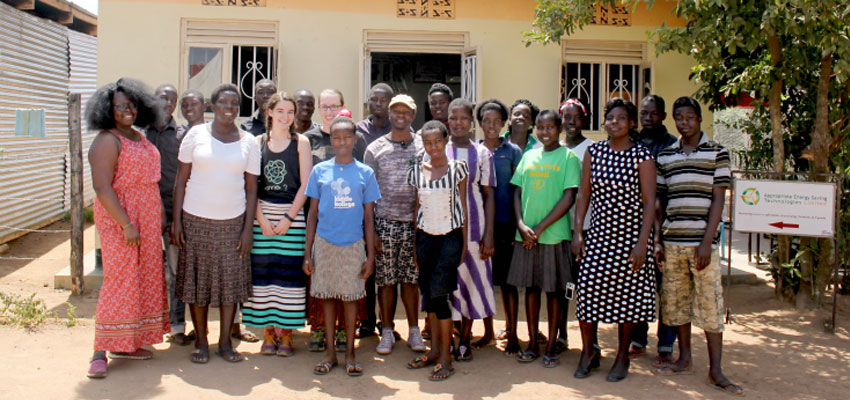
Over the course of the January Independent Activities Period, we had the opportunity to travel to Uganda as a continuation of our class in the fall: D-Lab: Development. D-Lab: Development was a diverse class of about 40 students, including students from multiple schools and across multiple majors, in which the class learned about all aspects of development work. The class included case studies on a variety of past development projects around the world and we planned development projects of our own. The class was split into small groups that were assigned projects in different countries. Rachel Galowich ‘18, Tim Manganello ‘17, Maddie Haas ‘17, and I (Drew Beller ‘18) were assigned to work in Uganda along with our team leaders D-Lab staff member Nai Kalema and graduate student Lauren Bustamante. We were also fortunate to be joined by Joy Lee ‘18 who was working with the MIT Engineers without Borders program to perform a needs assessment on recycling low density plastics.
While we were in Uganda, we worked on two projects with our partner Betty Ikalany in the Soroti district. Betty is an entrepreneur who has started her own charcoal briquette and cookstove manufacturing business as well as TEWDI (an NGO focused on helping women and children in poverty stricken areas). The first project (led by Rachel and Maddie) was an innovation workshop aimed at teaching students ages 10-18 about the design process and introduce them to a variety of STEM topics. Our second project (led by Tim, Joy, and me) was working to improve the ventilation of Betty’s charcoal grinder and help teach her team about the design process as well. Overall, the trip was a lot of fun and a unique experience that I believe we all will remember the rest of our lives. We met amazing people, ate amazing food, and hopefully had an impact on the community we worked with.
Innovation Workshop
The first day of the innovation workshop, we were greeted by more than 60 young adults from around Soroti. Over the course of the first week, we introduced our students to each phase of the design process, including methods of how to conduct interviews to gather information and assess community needs, brainstorm effectively, and choose ideas to further develop. This culminated in a day-long hackathon on Friday, where we challenged our students to use the design process to innovate an efficient way to light cook stoves.
Throughout the first week, each of us got to share lessons and activities in areas of our expertise. Tim, Drew, and Joy gave guest lectures on chemistry, electronics, and biology, followed by fun activities involving pH testing, potato LED circuits and gumdrop DNA. Maddie and Rachel both led favorites from our departments back at MIT: students launched water rockets and built structures out of spaghetti and marshmallows.
On Monday of the second week, we gave each team the chance to present the results of their hackathon project. Then, it was time to begin working on team projects! Students spent the rest of Monday brainstorming. By Tuesday morning, we had a list of 11 projects:
- White Team: Charcoal Refrigerator
- Pink Team: Biodigester
- Red Team: Forged Aluminum Saucepans
- Orange Team: Brick Oven
- Yellow Team: Drip Irrigation System
- Lime Team: Solar Dryer
- Green Team: Eggshell Crusher
- Turquoise Team: Mosquito-Repelling Jelly
- Blue Team: Sponges
- Purple Team: Vacuum Cleaner
- Lavender Team: Mosquito Repelling Candles
On Tuesday and Wednesday, we pushed students to apply aspects of the design process we discussed throughout week one. Students came up with lists of stakeholders in their projects and potential interview questions. They sketched dimensioned drawings and made 3D sketch models of their designs out of paper and tape. At the end of the day on Wednesday – after many exhausting trips to town – we were able to begin handing out materials, but only after students showed us their progress, and created a schedule of how they would budget their remaining time. It was incredible to watch their projects take shape, and then present their prototypes to friends, family, and distinguished community members with confidence.
Our goal was to engage local youth in creative capacity building so they could design and build technologies addressing issues prevalent in their community, and inspire them to explore topics in STEM. We definitely succeeded with the latter – our students were very engaged in the science lectures and accompanying activities, and some even approached the guest instructor after class to learn more about the topics they had covered. Many of the final projects were of high quality, but we had to push students through the correct brainstorming sequence more than we had anticipated, and help them understand that every solution must have a clear link to a community problem. We think there should be more emphasis placed on this perspective in upcoming workshops.
Technical Project (Charcoal Grinder Ventilation)
The largest problem we were able to identify was that the fine ground charcoal dust coming out of the charcoal grinder was coming out much too fast. As a result the small factory would quickly fill with a thick cloud of charcoal dust that was not a suitable work environment. This ventilation problem was commonly solved by other manufactures in the area by adding a large and complex fan and duct system to carry the dust away. We challenged ourselves and Betty’s team to come up with a low-cost, non-invasive way to improve the ventilation through a solution without any moving parts.
Our first week was spent prototyping a variety of ideas and working through an ideation and brainstorming process with Betty’s team. As we iterated and failed, it was hard to convince Betty’s team that we were making progress. They often laughed at our prototypes (made from pieces of scrap metal, old t-shirts, and duct tape) and were more interested in the complex fan system that other manufacturers in the area were using. By the end of the week, we started to have our first successful tests using a combination of ideas and Betty's team became more interested in the approach. Once they saw the potential of prototyping and trying new ideas they quickly got on board. From our first successful test on the Thursday of our first week to one week later when we left, Betty’s team really drove what we were working on and became very involved in ideation and testing.
Our final design involved adding a cloth tube as an extension to the output chute of the grinder. This helped to slow down the flow of charcoal dust and also allowed the grinder to deposit right into another collection bag. The addition of this cloth tube also caused a back flow of air and caused charcoal dust to come out of the input to the grinder. To fix this problem, we added a long chimney with a cloth filter on the end. Very little dust comes out of the chimney, but it does allow for more airflow. We found that with the chimney we solved the problem of charcoal dust coming out of the input. We also believe that having a large chimney acts as a sort of depressurization area, where the airflow and charcoal dust can slow even more before coming in contact with the outside environment. The final modification we made was to raise the grinder 30 inches into the air to allow for a collection bag to be placed directly under the output.
We were able to manufacture the entire extension and chimney assembly on site at Betty’s house with the help of her cookstove team. The extension was made out of .8mm steel, which was then taken to town to be welded onto the grinder. We also used a local tailor to make us the correct size cloth tube.
We weren’t able to see our final design being run in a full production day, but hope that we will receive good feedback soon. More important, we worked closely with Betty’s team from ideation to prototyping to testing to manufacturing the final product. We hope that the lessons we learned by working together and through this ventilation project will help them fix any problems they encounter in the future as well as improve on things that already exist.
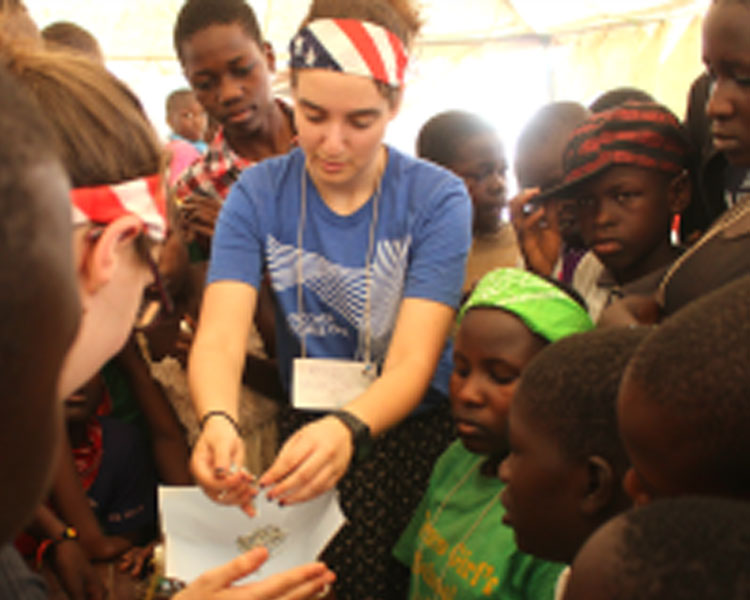
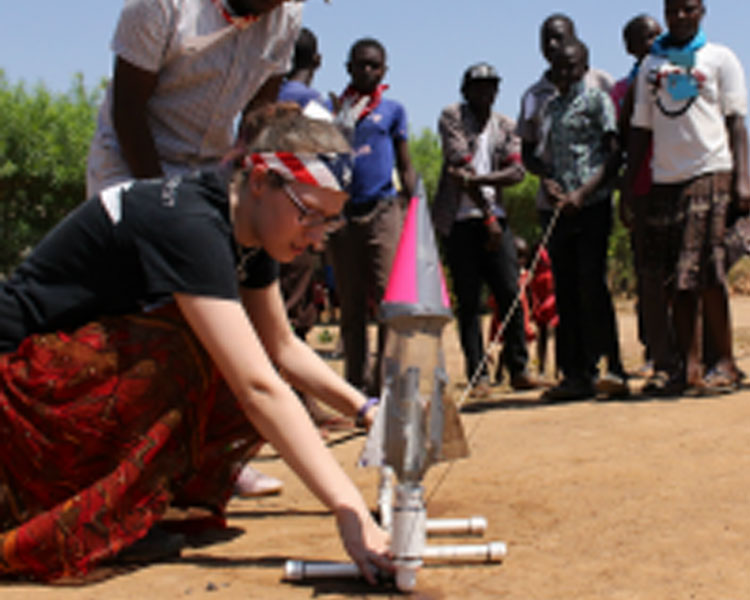
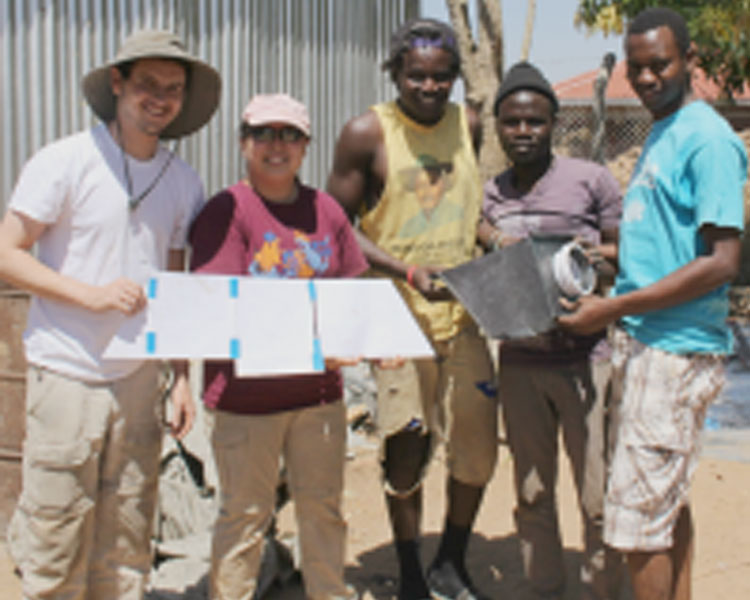
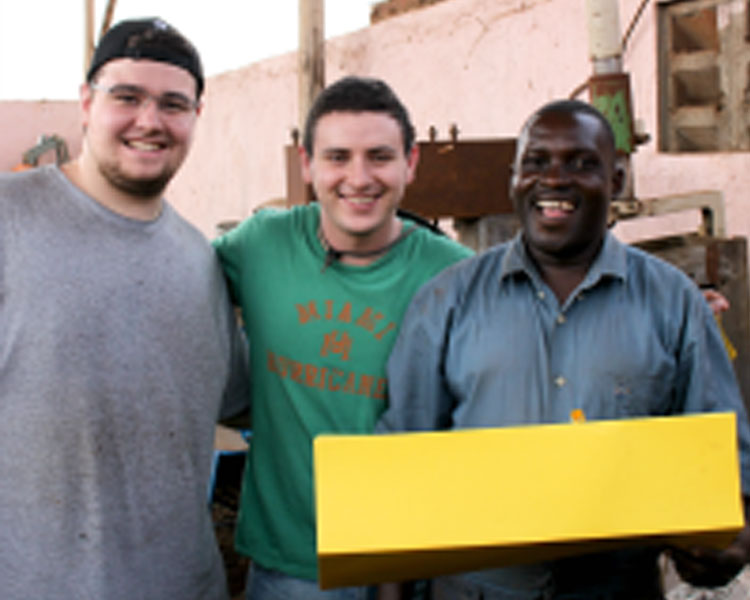