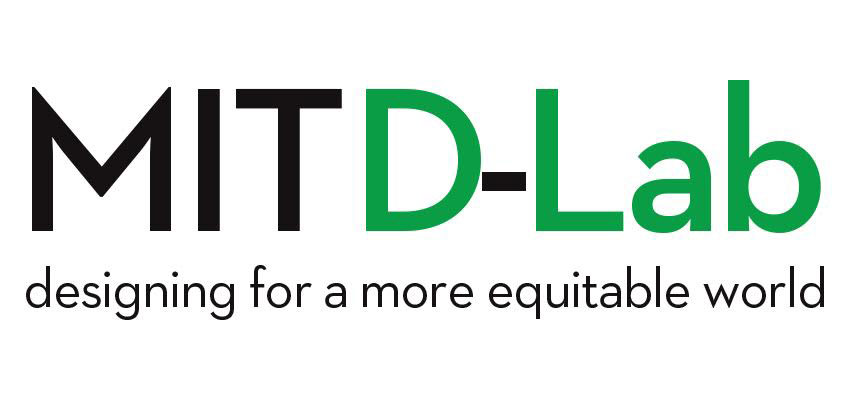
In August, I made my fourth trip to Tanzania. While my previous work has been centered around Arusha, this trip brought me to Dar es Salaam for the first time. After several weeks in Arusha, connecting with partners for what will hopefully be a D-Lab IAP trip, I took an eleven-hour-long Dar Express bus ride to the former capital and largest city in Tanzania. The bus is known for serving a soda during the trip, and I enjoyed my Fanta Orange as well as the truly astonishing views out the window as we drove across the country. I nearly missed the bus after our lunch stop, so I got to do the “jump into a moving vehicle” thing for the first time (it was moving slowly and quite fun), and continued on my journey.
After I reached my hostel in Mbezi Beach (outside of Dar city center) in the evening, Potnis, the co-founder of ARTI-TZ/ARTI Energy, was kind enough to welcome me with a delicious dinner out. ARTI Energy identifies appropriate renewable energy technologies and introduces them to Tanzania, “building production and sales capacity and public awareness through training and equipping beneficiaries and consumer sensitizing campaigns.” In addition to their work making charcoal from agricultural waste, they promote and sell solar lighting systems and kitchen waste biogas systems.
The following day I visited the ARTI office in Mbezi Beach in the morning and then went to see several field sites in the Bagamoyo district for the rest of the afternoon. Joseph, a long-time friend of D-Lab and the International Development Design Summit, had come out from Arusha with me to help with translation and more; it was great to have his company on the trip. Our goals for the five days in Dar were getting to know ARTI and seeing their work, including their charcoal-making progress, and doing market research on charcoal use in Dar.
ARTI currently has one CBE, or community-based enterprise, that is producing charcoal. The CBE, Bagamoyo Briquette Company, collects char powder from local producer groups (up to 30 people working together) who have been trained in the production process -- how to fabricate kilns and carbonize different agricultural waste materials. Coconut shells, husks and wood shavings are some of the most common materials. The CBE then makes the binder (using ground, dried cassava skins), makes the wet mixture, uses an extruder to make the briquettes, and dries and packages them. They had just purchased a giant extruder from China and hope to start selling their charcoal in supermarkets soon, pending approval by the Tanzania Revenue Authority.
For the rest of my trip, I was interviewing different charcoal stakeholders with Joseph. I was connected to some through ARTI, and others through Joseph’s friend, Eveline. It was sometimes difficult to get people to agree to be interviewed – especially with the unfamiliar consent form – but by the end everyone was very sweet and thanking us! Talking to one woman who had tried a different alternative charcoal (apparently made from sunflower waste products) was especially interesting.
All in all, I enjoyed my first trip to Dar. Many people warned me about the traffic I would encounter, but as I spent most of my days away from the city center it was less an issue for me. I also loved being so close to the ocean, and managed to have a dip in the Indian Ocean on my last day before flying out. I hope to have the opportunity to return and work with ARTI again!